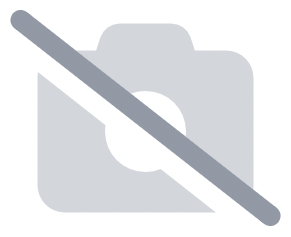
In the light of the Grenfell tragedy, the spotlight has been shone on fire safety with the result that building regulations are becoming much more stringent, and building products are coming under more scrutiny. As the first manufacturer to launch fire-rated downlights back in 2005, with our award-wining FlameGuard® fire protected and acoustic rated products – we have had years of experience in developing, modifying and improving our range of products to ensure they meet the latest requirements.
Why is fire rating required?
A standard house in the UK usually has two floors, and where there is living space above, the wooden floor construction with plasterboard ceiling must pass stringent fire tests. In these properties, the complete floor/ceiling construction between the two floors, must withstand a minimum of 30 minutes of fire to 1) prevent rapid fire spread which could entrap occupants of the building, and 2) to reduce the chance of fires becoming large, on the basis that large fires are more dangerous, not only to occupants, fire and rescue service personnel, but also to people in the vicinity of the building. Where there is no living space above, for example loft space, no fire rating is required. However, we would still recommend fire-rated downlights in the event this area should be converted to a living space at a later date.
The more floors in a building, the longer the fire protection/compartmentation has to last. In a three-story building with the loft converted to a bedroom, the floor constructions must comply with 60 minute fire rating to give enough time for the occupants to evacuate in the event of a fire.
Downlights and fire rating
The floors and ceilings will have passed fire testing as a complete floor, but once an aperture for a downlight is made, the fire barrier is broken. A standard open back downlight allows the fire, vapours and heat to penetrate the floor space and can lead to collapse before the required times of 30, 60 or 90 minutes.
A fire-rated downlight uses a sealed steel body, together with an exterior intumescent strip around the unit. In the case of a fire, these elements separate the room from the ceiling void, preventing the spread of fire. The intumescent material helps stop the fire, heat and vapours from spreading into the void.
Downlights and fire testing
Our testing is carried out to strict BS standards and there are a number of building regulations that cover the testing of downlights:
BS 476: Part 21: 1987 – Fire tests on building materials and structures. Methods for determination of the fire resistance of loadbearing elements of construction
BS EN 1365-2: 2014 – Fire resistance tests for loadbearing elements. Floors and roofs
BS EN 1363-1: 2012 – Fire resistance tests. General requirements
All our fire tests are carried out by independent testing specialists BRE (Building Research Establishment). BRE Global is a UKAS accredited testing laboratory. They can comprehensively test, predict and assess the fire performance of products and materials to British, European, Marine and International fire-test standards. BRE Global operates one of the largest fire research and testing laboratories in Europe. Their facilities include a state-of-the-art Burn Hall (one of the largest in Europe) capable of staging 10 MW (9m x 9m hood) calorimeter fire tests, and a large custom-built facility for fire resistance tests of floors, walls, beams and columns.
BRE tests our fire-rated downlights under real world conditions. This starts with the construction of the floor to fit the furnace (4.5m x 3.5 m approx.) whilst following the material manufacturer’s construction guidelines for the fire rating required. The joists, floor board and plasterboard are assembled, with the apertures then cut and the downlights fitted. The downlights have to be spaced at recommended distances to give an account of real-life installations in a worst-case scenario.
Once constructed, weights are added to the floor to simulate the weight of furniture, etc. The floor is lifted into place on the furnace, with the heat thermocouples added to the required elements. The furnace is heated by gas burners, to over 1000â°C and the furnace temperature is regulated and monitored during the testing. The temperate during the test can exceed 1,000â°C.
If more than one layer of plasterboard is fitted (e.g. the 90-minute fire test), the first layer can fall without being deemed a failure. The main contribution to an early failure is a hot joint on the floorboards. This is mainly due to vapours and heat build-up within the floor void exceeding 300â°C where ignition is only required. The test can stop in the event of earlier failure - whether the required time has elapsed or until the floor construction collapses.
At Scolmore we design our products to withstand the rigorous testing that is necessary to meet the requirements of the BS standards governing their safety, and wholesalers should be using this information when advising their customers on the right products for the project they have in mind. With a Scolmore fire rated downlight they have the assurance that this is a quality product that has undergone all the required and rigorous testing and is a reliable and safe product to use.
Some manufacturers will state that their products have a 90 minute fire rating. However, that doesn’t always mean that they will meet the requirement for 30 or 60 minute ratings. Each rating has its own test, so they should have passed all three tests to ensure the full rating requirement.
Scolmore has produced a CPD training module – ‘Downlights and testing for fire rating’, and this is available for delivery on request.